Beep, Beep, Beep! The Benefits of Barcoding
- Christine Lee
- Nov 27, 2018
- 4 min read
Updated: Dec 30, 2024
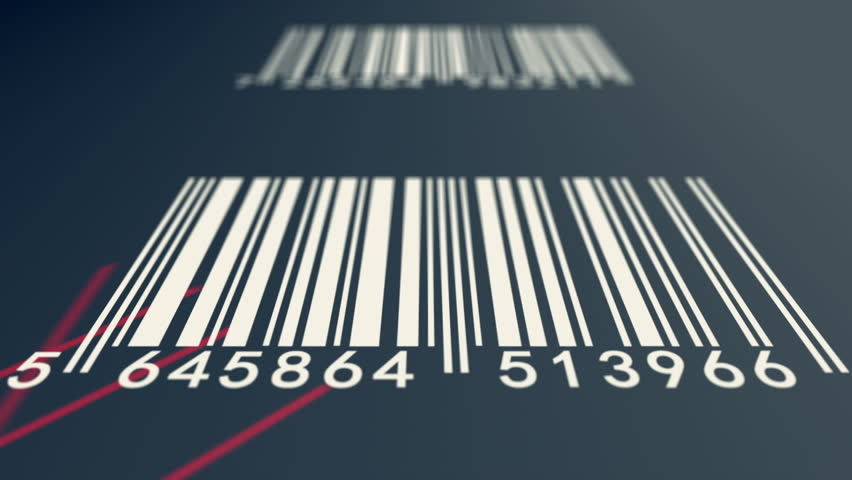
The constant beeping of barcodes scanning in a supermarket can drive some people nutty. But what would your local shopping centre look like today without barcodes? As we head into the busiest retail period of the year, where it is estimated Australians will spend $51.5 billion in retail stores in 2018 (Roy Morgan/Australian Retailers Association, 2018), let's talk about the benefits of implementing barcoding for your business.
When I was eight years old, my life ambition was to work in Coles Supermarkets as a checkout operator. Barcodes and numbers were an endless fascination for me as a child. I had a wooden cash register, drew a big red star on the lid of an ice-cream container to represent the optical laser reader, and used that as my pretend barcode scanner. I'd play shops with my brother and scan empty food boxes and drink containers through my cash register.
Fast forward almost twenty years, and funnily enough, here I am working in a job that involves barcodes. They may just be a series of abstract looking black and white bars with a random sequence of numbers underneath, but what are they, why do they matter, and how can they help your business?
A Short History of Barcodes
The first barcode reader was built in 1952 by Bernard Silver and Norman Joseph Woodland. The original intended use for barcodes was to identify railroad cars. It wasn't until a few years later that they were used in the retail space.
The concept of the UPC (Universal Product Code) was first introduced at Marsh Supermarket in Troy, Ohio in the early 1970s. A supermarket manager wanted to get shoppers through his store more quickly, and make stocktake much easier than a pen and paper method.
Some of the first barcodes looked like bullseyes - a series of concentric circles, and not the rectangular barcodes we know today. However, these were difficult to print, and resulted in reading errors from mis-scans or misalignment.
The UPC was not an immediate success - until larger merchandisers such as Kmart and Wal-Mart in the United States adopted the technology. The instant identification of items with a single click of a laser scanner had value for businesses to see which items were moving the fastest.
Benefits of Barcoding
Instant product identification
The time it takes to search for a product on a computer by typing in product names or product codes can be more than a few seconds, especially if your inventory consists of thousands of different products. With barcodes implemented, this time can be reduced to milliseconds, by using a barcode scanner to identify a product instantly.
Quality assurance
Barcodes are a unique identifier that can be used for batch or serial tracking. Particularly in food manufacturing, industrial manufacturing and the medical industry where traceability is important, barcodes can be used as a unique identifier in the case of a product recall or manufacturing fault.
Efficient warehouse management
Use a scanner in your logistics and dispatch department to ensure the correct items are being picked and packed by your warehouse staff. Scan barcodes from pick lists and match them to items being taken from the shelf to ensure accurate order dispatch. Many cloud systems offer mobile-based WMS (Warehouse Management Solutions) where employees and warehouse managers can use their mobile devices to scan barcodes.
Insight, reporting and accurate inventory control
When the correct items are picked, it is then easier to see at a glance which items are running low, and what stock quantities should be reordered. Theft or loss can be more easily recognised when controlled inventory measures are enforced, and items received in can be easily catalogued when a shipment arrives with barcode printing available at a purchase order level.
Facilitate stocktakes Gone are the days of spreadsheet-based stocktakes and handwritten stock figures. By using a barcode scanner, stocktakes can be done in around half the time that a manual stocktake goes for. Many scanners use Bluetooth technology to wirelessly pair with your computer or tablet, so stock counts can feed back to the main computer or your tablet while you're physically walking to each shelf and counting.
Customer satisfaction and service speed
Time is money these days, and neither you or your customers want to be kept waiting by slow loading systems or product searches. It also ensures that every item is accounted for as it is scanned through. Barcodes can be added to the footer of receipts to facilitate the lookup of previous sales in the event of a return or exchange.
Streamlined stock
Get rid of handwritten price stickers, or costly label refills for your pricing tag gun. A consistently sized barcode label adds a more professional and uniform appearance to your products. As well as displaying a barcode on labels, a product name and price can also be added to the barcode label, giving the customer some more informative information and making it clear what they are purchasing.
Would barcoding your stock save you and your staff time with sales and stocktakes? Want to get a head start for 2019 with a streamlined barcode scanning solution? We can advise on the optimal software and hardware setup that's just right for your business. Register your interest in implementing Barcoding and Labelling at our Barcoding Services page, and a Solutions Consultant will be in touch to see how we can implement barcodes for your small business.
Comments